Japan's liquid rocket engine, which is highly reliable worldwide,
It is about to evolve from the mainstay H-IIA / B to H3.
Professor Hiroyasu Manako, who studies the key "combustion",
Utilizing his experience as a rocket development engineer, he aims to lead from basic research to practical use.
Leader of Japanese rocket technology
H-IIA liquid rocket engine
A rocket that launches a supply machine for artificial satellites and the International Space Station into space. In Japan, the first large rocket HI was launched in 1975. The engine at that time was made in response to the introduction of technology from the United States, but with this launch, the development of domestic rocket engines accelerated. In 1994, the first test machine of the H-II rocket equipped with Japan's first purely domestic one-stage rocket engine "LE-7" was finally launched. After that, since the improved H-IIA was launched in 2001, the H-IIA / B has been launched 47 times by October 2018, of which 46 have been successful. The success rate is 97.9%. Considering that the world launch record is about 90%, the high reliability of the H-IIA / B rocket can be seen.
Japan's new rocket
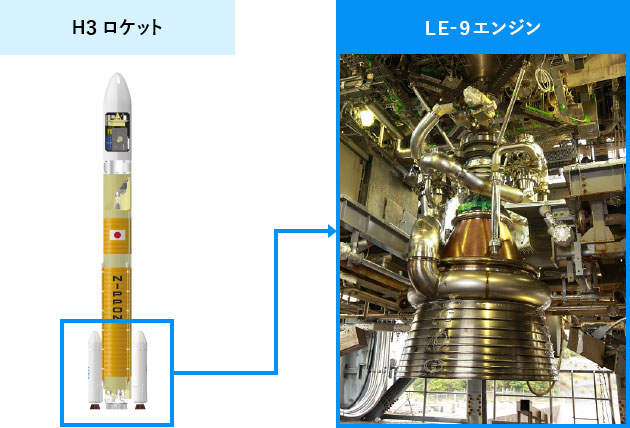
source:
(Left) http://jda.jaxa.jp/result.php?id=f08bdde84676a4a0b3eaa3a0fd50ce12&adminflag=1
(Right) http://www.rocket.jaxa.jp/engine/le9
Professor Hiroyasu Manako of the Department of Department of Aerospace Engineering, Faculty of Faculty of Science and Engineering and Engineering is one of the people who supported the technology. During his previous job as an engineer at Mitsubishi Heavy Industries, he was involved in the development of the "LE-7A" from the start of development to mass production, and has been dedicated to the development of liquid rocket engines.
"I was interested in space because of the animation I saw when I was a kid, and at university I was researching hydrogen combustion in a combustion system laboratory. From that time, I wanted to be involved in the development of rocket engines. After graduating from university, I was involved in the development of a liquid rocket engine at Mitsubishi Heavy Industries. I have witnessed the launch of the rocket many times. The moment I took off safely is very moving. "(Professor Manako)
There are two types of rocket engines, one that uses liquid fuel and the other that uses solid fuel. The liquid rocket engine that Professor Manako is studying has the advantage of high control performance and good fuel economy, such as being able to ignite once and then turn it off, reignite it, and finely adjust the output. On the other hand, although a solid rocket engine can ignite only once, it has a large thrust. Some rockets carry either liquid or solid rockets, but large rockets around the world often carry both liquid and solid rocket engines. Use a strong solid rocket engine where thrust is required immediately after launch, and switch to a liquid fuel engine that is easy to control when it becomes lighter with solid fuel.
The mysterious mechanism of "combustion vibration"
Unravel through combustion experiments
The "LE-7A" mounted on the H-IIA and H-IIB rockets uses a staged combustion cycle that burns in two steps. In the staged combustion cycle, a part of liquid hydrogen and liquid oxygen is burned in advance in a sub-combustion chamber called a preburner, the combustion gas turns the turbine of the turbo pump, and then the remaining gas remains in the gas that drives the turbo pump. Add oxygen and burn again. This method has extremely high performance and has been adopted in the main engine of the Space Shuttle, which has greatly contributed to the breakthrough of rocket technology. However, rocket technology has not yet reached its goal.
There is a worldwide movement to improve rocket launch costs and reliability.
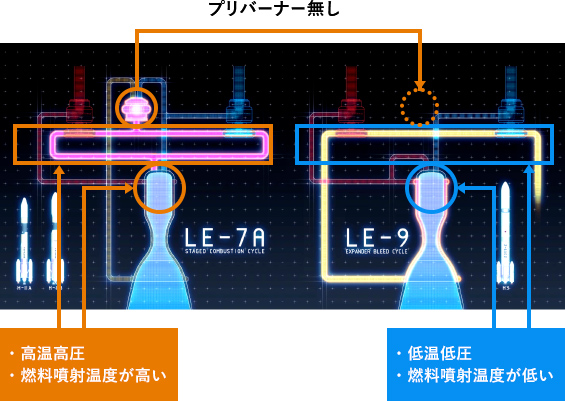
Left: Staged combustion cycle, Right: Expander bleed cycle
source: https://www.youtube.com/channel/UCfMIdADo6FQayQCOkLYGhrQ
The "LE-9", which is being developed by JAXA as the engine of the H3 rocket, which is considered to be Japan's next major rocket, generates 1.4 times the thrust of the "LE-7A" and at the same time realizes low cost and high reliability. I'm trying to make you. Currently, Professor Manako is working on research with an eye on "LE-9."
Professor Manako is paying attention to the phenomenon called "combustion vibration". It is a resonance phenomenon that occurs when the heat and pressure generated in the combustion chamber strengthen each other's fluctuations, and if the pressure fluctuations due to combustion vibrations become large, there is a risk of damaging the engine. The expander bleed cycle used in the "LE-9" has a structure without an auxiliary combustion chamber. The combustion chamber and nozzles are cooled by ultra-low temperature liquid hydrogen, and the turbine is powered by the fuel that has become hot due to the heat exchange generated at that time. turn. Since there is no auxiliary fuel chamber and the number of parts is small, the cost is reduced and it is said that combustion vibration is likely to occur while it has the advantage that abnormal combustion is unlikely to occur, so we will focus on clarifying this phenomenon. I want to.
"The expander bleed cycle does not reuse the heat that turned the turbine in the first combustion like the staged combustion cycle, but exhausts it as it is, so the fuel injection temperature is low and combustion vibration is likely to occur. In the mechanism inside the double circular tube, which is an element that injects and mixes liquid oxygen and liquid hydrogen, the gap (groove) from which fuel comes out becomes narrower, which makes the element eccentric and more susceptible to foreign matter. It was found that there is a risk of melting the combustion chamber, such as spilling. As the next step, we are elucidating the phenomenon of combustion vibration and researching and developing a device called a resonator that suppresses combustion vibration. (Professor Manako)
research content
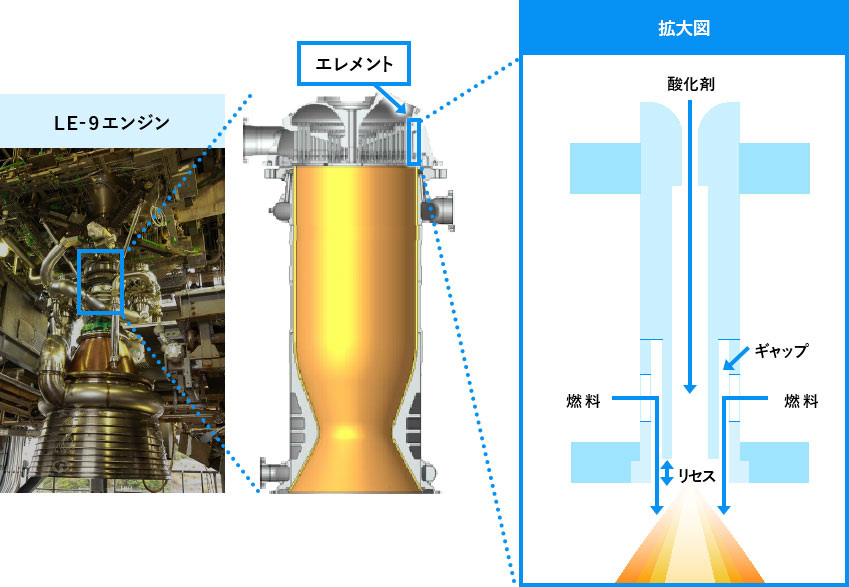
We are working to elucidate the mechanism of combustion vibration. (Photo courtesy of JAXA)
Source: Masaki Adachi et al. ISTS 2015
The actual rocket engine has a structure in which hundreds of elements are bundled together, but Professor Manako's laboratory manufactures a combustion experiment device using one element. We started a combustion experiment at room temperature using gaseous hydrogen and oxygen. Furthermore, we are verifying the structure and arrangement of resonators that absorb the sound of the target frequency band by generating a resonance phenomenon that simulates combustion vibration with the sound emitted from the speaker.
From basic research at university
To the rocket engine of the future
In recent years, Japanese rocket technology has developed as much as the United States and Russia. The "LE-9" by the expander bleed cycle will also be a world-class rocket engine as a technology unique to Japan. Professor Manako says that basic research at the university will be an important step toward that end.
"At a company's development site, it is a priority to reach a set goal within the deadline. Therefore, even if something goes wrong, there is no time to explore it, and it is certain to explore other methods. However, the basic mechanism of combustion, including combustion vibration, has not yet been elucidated. If we can establish a technology to clarify and suppress the mechanism of combustion vibration, a higher quality rocket engine will be used. The basic research we are currently working on may be applicable not only to the new rocket engine in front of us, but also to future rocket engines. "(Professor Manako)
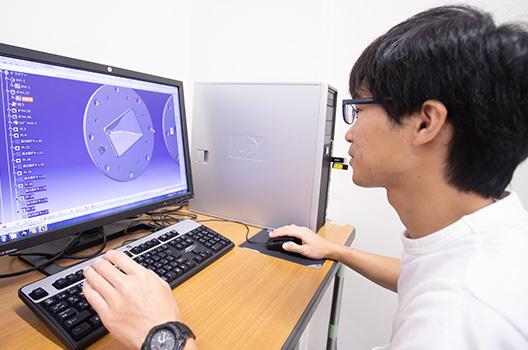
It has been three years since I moved to Teikyo University from the rocket development site of a company. At the university, cross-sectional connections with researchers in different fields are also inspiring. The students in the laboratory are also kind and instructing. Professor Manako is aiming to establish a theory that will lead to the future and to produce human resources who will lead the next generation, with an eye on the further development of liquid rocket engines.
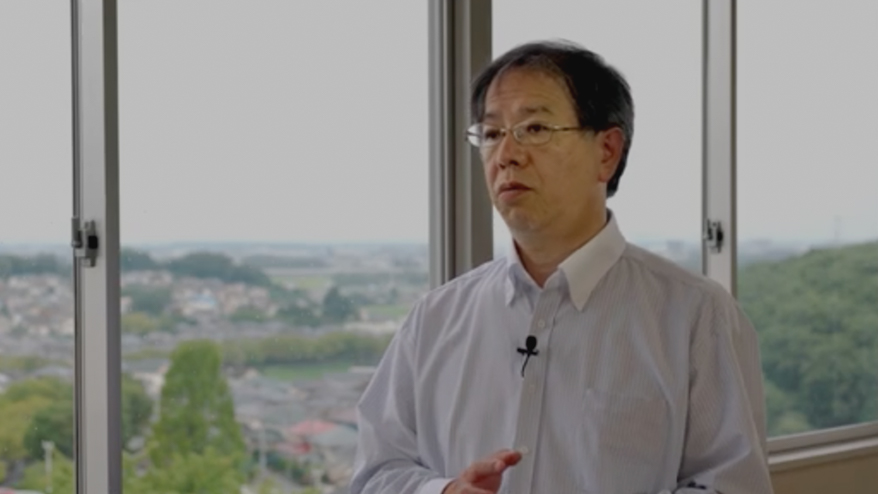